Resources
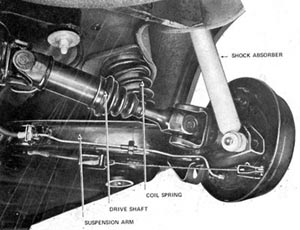 |
This diagram was taken out the Datsun 1600/510 workshop manual. I have made a PDF document of the 'Rear Suspension - Sedan Specifications' section of this book, its pretty large but well worth reading if you don't have access to your own manual.
Download it HERE (right click and 'save target as') |
This diagram was taken from a document I found on the internet about different types of uni joints - to find out what it had to say about the type used in your datto - please click here and a popup window will open.
|
Depending on what diff you are running, universal joints are often seen to be the weak point in a driveline. The standard datto 1600 rear end with R160 diff has 4 on the half shafts (one on each end) and then 2 on the tailshaft. If you are experiencing a 'clunking' noise and sensation on taking off and changing gears, then it is worth investigating the rear end to see if the uni's are to blame. To do this simply jack up the back of the car (placing blocks in front of the front tyres to prevent the car from rolling) and grab the half-shafts and try to rotate them back and forth quickly. If there is any play in the shaft (ie. the middle part of the shaft moves and the ends don't) then the universal joint is probably stuffed, and will need replacing.
Items needed
- jack, car stands and blocks
- new uni joints (about $50 from Repco)
- a couple of biggish nuts (about 15mm diameter)
- a decent heavy duty bench vice
- WD40, RP7 or other brand of lubricant
Tools needed
- wheel brace
- basic toolkit inc. 2x12mm spanners
- large round file
- pointy nosed pliers
- big hammer
- grease gun
Procedure
To
remove the half-shaft, make sure the back of the car is securely jacked up,
preferably on car stands, then remove the wheels. Unbolt the end of the shock
(1x12mm nut) and let it swing free, then undo the 4 bolts that hold the end
of the half shaft (the yoke hub) in place. Using 2x12mm open ended spanners
against each other is the best way to do this. There are also 4 similar bolts
that hold the other end of the half shaft onto the diff, undo these to let the
entire shaft come off freely.
Next comes the 'fun' part - getting the old uni joint out of the end of the
half shaft. There are clips that hold the joint in place so try and manouvre
these out first, you may need to spray the area with some WD40 to clean and
loosen the components first. If you can't get the clips out, hold the end of
the half shaft on the bench and hit the floating yoke hub with a big hammer
until it starts to come out; then try and remove the clip again as it should
be easier now. Once the clips are gone it's a simple matter of bashing the crap
out of the old uni joint until it comes out. Alternately put the joint in the
vice and put a big nut on one end of the uni and just squeeze. Sounds a bit
obscure I know but once its there in front of you its pretty easy to work out.
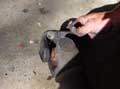 |
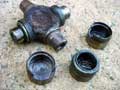 |
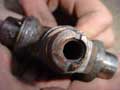 |
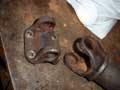 |
The old uni joint in place at the end of the half shaft. |
The bearing caps with munched or sometimes non-existant
roller bearings. |
The end of the cross piece (usually perfectly round)
had been worn away by lack of bearings and mass amounts of friction. |
This is what the end of the half-shaft should look like with the old uni
joint removed. |
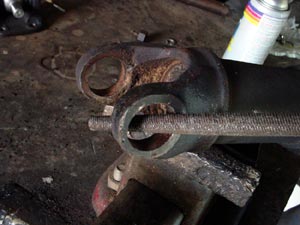 |
Once the old universal joint is out, file the edges of the
holes on the yoke arms to make sure there are no sharp bits to damage your
new uni's, and to make sure they will slide in easily.
The new universal should look like this one, plus 4 clips
and a grease nipple that are not visible in this photograph. A hint to
those who are ordering them from a place like Repco - make sure you specify
HALF SHAFT or DRIVESHAFT universal, because most employees automatically
assume you are after a tailshaft uni, as they may be unaware that 1600's
have independent rear suspension. The price difference is quite substantial - I was quoted $22 for a tailshaft
uni by accident, then arrived at the store to find out the ones that I
wanted were actually $58! I managed to talk them down to $45 though so
that was ok. ;) |
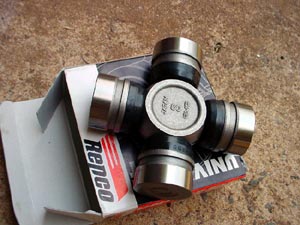 |
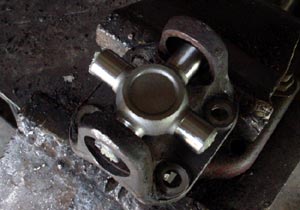 |
Step 1
Slide the trunnion bearings off the end of the cross pieces and put them
aside. Place the end part of the half shaft on the bench and put the yoke
hub and cross piece in position. |
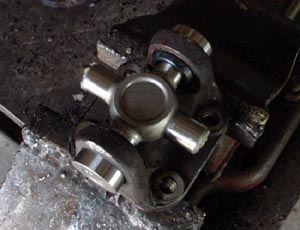 |
Step 2
Slide 2 of the trunnion bearings onto the ends of the cross piece, they
should sit firmly in place. Be careful not to disturb the roller bearings
inside. |
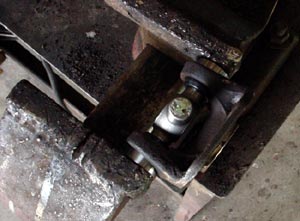 |
Step 3
Put the uni in the vice with only the trunnion bearings in contact with
it as shown. Slowly tighten the vice - the bearings should pull in and
slide onto the cross piece. |
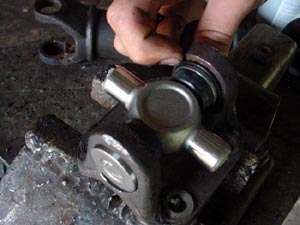 |
Step 4
This is what the joint should look like after the bearings have been
pushed on. The sir-clip on the far side has been clipped on and is pretty
much in the correct position, you can just see it at the end of Andrew's
finger.
The bearing on the near side is not completely lined up yet; it needs
to be pushed in that little bit further soit sits flush with the yoke
arm. |
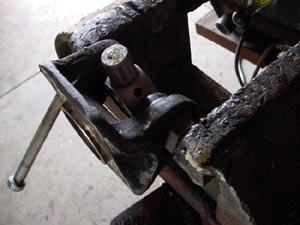 |
Step 5
We can do this by putting the joint in the vice again but this time using
a large nut (a little bit smaller than the end of the bearing) placed
next to the end of the bearing, so when the vice squeezes them on the
yoke arm, it doesn't get in the way.The remaining sir-clip can then be clipped on just inside the yoke arm
- you will see a groove for it to sit in (also have a look at the previous
photo). Use pointy nose pliers and a flathead screwdriver to make sure
both clips are secure. |
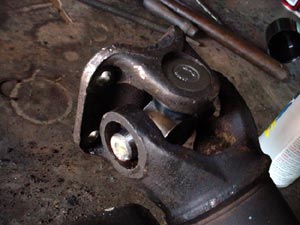 |
Step 6
With one side of the joint completed, now get the main part of the half
shaft and position the cross piece inside the second yoke arm. |
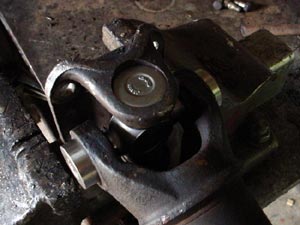 |
Step 7
Follow through steps 2-5 to fit the bearings onto the end of the cross
piece.
Make sure ALL 4 clips are in the right position and as far in as they
will go!! Failure to do this may cause the bearings to work their way
off the cross piece. |
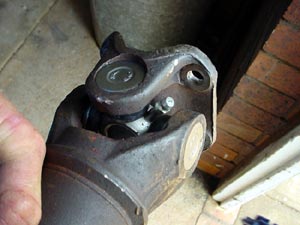 |
Step 8
Lastly, screw in the grease nipple and fill 'er up!
The joint is now complete and the half shaft ready to bolt back on.
Happy (and safe!) motoring. :D |